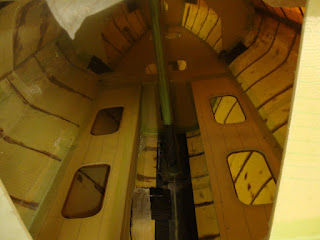
Interior is ready to get boat out of the mold. Lots of firewood for the winter.....

Bottom of boat.

Filling holes and seams to infuse the bottom.

Deck infused, I choose to do it in two tempies, since working with the boat on the side makes it quite high.
Cockpit floor reinforced with layers of unicarbon both sides. An other layer of glass will be added once the stern is ready.
New roofing for the shed, the old one leaked a lot. This is a 15 mm plywood with prefitted tar roofing, self adhesive overlayes, quite smart, and very easy to install, thanks Jacob for the materials, and Grus for helping me.